Retaining walls and mass concrete underpinning are vital construction and landscaping techniques that certify stability and structural reliability. They serve different purposes but are often used together in projects where ground constancy is fundamental, such as sloped areas, basement construction, or renovation of current foundations. In this comprehensive guide, we will discover these two methods, their purposes, materials used, methods of construction, and their significance in the building process.
Retaining Walls
A Retaining Wall in London is intended to hold or retain soil behind it. These walls are important in stopping soil corrosion and handling land in areas with extreme land or major height variations. Retaining walls allow the construction of level areas on slopes, protect structures from landslides, and support vertical or near-vertical grade changes.
Types of Retaining Walls
Gravity-retaining walls:
These rely on their mass and weight to resist the soil pressure behind them. They are usually built from heavy supplies like concrete, stone, or brick.
Cantilevered Retaining Walls:
These walls use a slab of concrete that extends into the soil, creating a “cantilever” that helps resist the lateral pressure of the soil. They need less material than gravity walls but a solid foundation and support.
Sheet Pile Retaining Walls:
Used in soft soil conditions or spaces with low wall height. They contain vertical metal, wood, or vinyl sheets pushed into the ground.
Anchored Retaining Walls:
These walls are anchored into the ground by cables or other materials, offering additional support against lateral pressure.
Materials for Retaining Walls
Concrete:
It is one of the most used materials for retaining walls, offering strength and durability. Precast concrete blocks or poured concrete can be used depending on the project size and requirements.
Stone and Brick:
Traditional materials that provide both function and aesthetic appeal. They work well for smaller walls but may require more extensive labour for installation.
Timber:
Frequently used in residential projects for smaller retaining walls due to its cost-effectiveness. However, it is not as hard-wearing or enduring as concrete or stone.
Gabion:
Steel wire baskets filled with stones are commonly used in landscaping to retain walls where drainage is a priority.
Construction Process for Retaining Walls
Site Evaluation and Design:
Assess the slope, soil type, and wall height. This will help you choose the right type of wall and materials.
Excavation:
The extent to which the wall will be built needs to be dug. The foundation must be deep enough for gravity walls to support the wall’s mass.
Foundation and Drainage:
The foundation, often made of compacted gravel, is laid at the base. Drainage systems are installed behind the wall to prevent water pressure buildup, which can lead to wall failure.
Wall Construction:
Depending on the wall type, materials are either stacked, poured, or anchored into place. Reinforcements like steel bars may be added to enhance structural strength.
Backfilling and Finishing:
Once the wall is constructed, it is backfilled with soil. Drainage pipes or gravel may be used to ensure proper water flow away from the wall.
Mass Concrete Underpinning
Underpinning is a process used to strengthen and stabilise the foundation of an existing building or structure. Mass concrete underpinning, one of the oldest and most used methods, involves extending the foundation depth or width by pouring concrete beneath the current foundation. It is often employed when the original foundation is unable to bear the load of the building due to factors such as soil subsidence, increased load from additional floors, or nearby construction that has affected the soil.
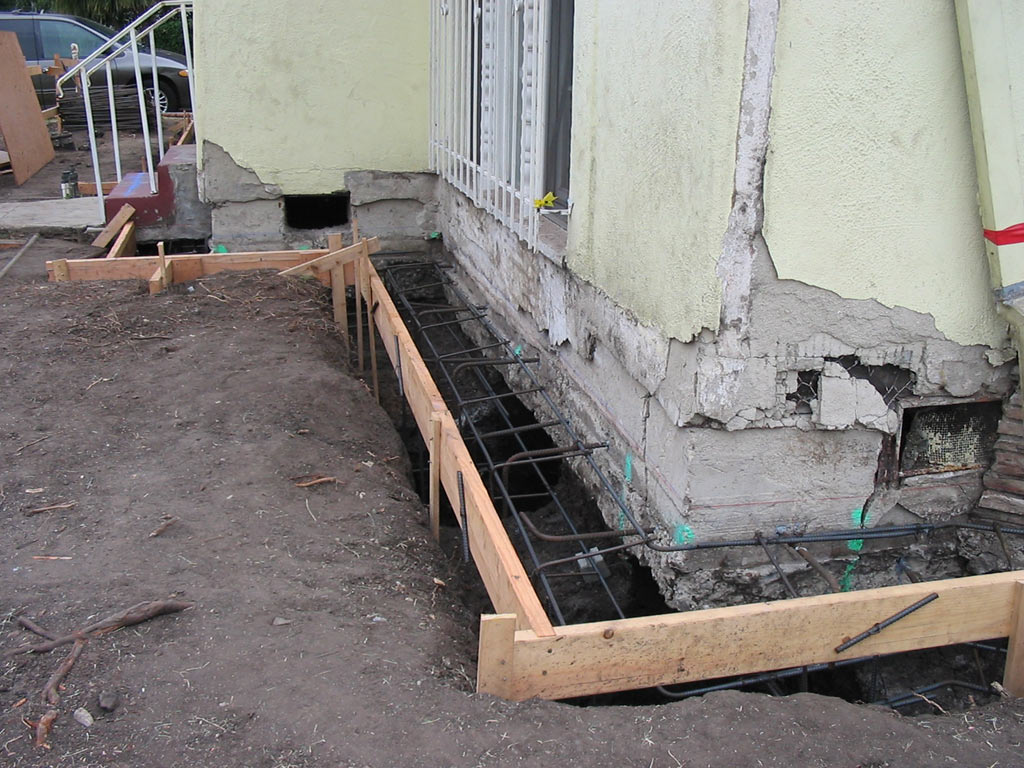
Mass Concrete Underpinning Process
Initial Assessment:
Engineers conduct a thorough site investigation to assess the condition of the foundation and soil. This involves checking the soil’s load-bearing capacity, determining the extent of underpinning needed, and designing the system accordingly.
Excavation in Segments:
Small sections (called “pins”) are excavated beneath the existing foundation to prevent the structure from destabilising. The size of each section is designed based on the building’s heaviness and foundation category.
Concrete Pouring:
After excavating each pin, concrete is poured into the cavity, extending the foundation downward. The concrete is allowed to cure before moving on to the next segment.
Layering for Additional Depth:
If a significant increase in foundation depth is needed, multiple layers of underpinning may be required. After each layer of concrete cures, excavation continues to deepen the foundation, followed by another pour.
Reinforcements:
Depending on the building’s requirements, reinforcements such as steel bars may be added to the concrete to strengthen the foundation further.
Backfilling:
Once all sections are underpinned and the concrete has cured, the soil is backfilled into any remaining spaces around the foundation.